
機(jī)械液壓傳動(dòng)基本原理,機(jī)械基礎(chǔ)液壓傳動(dòng)課程

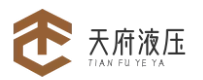
今天給各位分享機(jī)械液壓傳動(dòng)基本原理的知識(shí),其中也會(huì)對(duì)機(jī)械基礎(chǔ)液壓傳動(dòng)課程進(jìn)行解釋,如果能碰巧解決你現(xiàn)在面臨的問(wèn)題,別忘了關(guān)注本站,現(xiàn)在開始吧!
本文目錄一覽:
- 1、液壓傳動(dòng)的基本原理是什么?
- 2、液壓傳動(dòng)是什么原理?
- 3、液壓傳動(dòng)的基本工作原理是什么?
- 4、液壓傳動(dòng)的工作原理、系統(tǒng)組成是什么?
- 5、1.何謂液壓傳動(dòng)?其基本工作原理是什么?
液壓傳動(dòng)的基本原理是什么?
液壓傳動(dòng)是靠密封容器內(nèi)的液體壓力能,來(lái)進(jìn)行能量轉(zhuǎn)換,傳遞與控制的一種傳動(dòng)方式。液壓傳動(dòng)是以密封容器中的受壓氣體作為工作介質(zhì)來(lái)傳遞運(yùn)動(dòng)和動(dòng)力的傳動(dòng)。
液壓傳動(dòng)是以密閉管路中的受壓液體為工作介質(zhì),進(jìn)行能量的轉(zhuǎn)換、傳遞、分配和控制的技術(shù)。液壓傳動(dòng)工作原理可用圖1-1所示的液壓千斤頂工作原理來(lái)說(shuō)明。
工作原理:電動(dòng)機(jī)帶動(dòng)液壓泵從油箱吸油,液壓泵把電動(dòng)機(jī)的機(jī)械能轉(zhuǎn)換為液體的壓力能。液壓介質(zhì)通過(guò)管道經(jīng)節(jié)流閥和換向和閥進(jìn)入液壓缸左腔,推動(dòng)活塞帶動(dòng)工作臺(tái)右移,液壓缸右腔排出的液壓介質(zhì)經(jīng)換向閥流回油箱。
液壓傳動(dòng)是什么原理?
工作原理:電動(dòng)機(jī)帶動(dòng)液壓泵從油箱吸油,液壓泵把電動(dòng)機(jī)的機(jī)械能轉(zhuǎn)換為液體的壓力能。液壓介質(zhì)通過(guò)管道經(jīng)節(jié)流閥和換向和閥進(jìn)入液壓缸左腔,推動(dòng)活塞帶動(dòng)工作臺(tái)右移,液壓缸右腔排出的液壓介質(zhì)經(jīng)換向閥流回油箱。
液壓傳動(dòng)是靠密封容器內(nèi)的液體壓力能,來(lái)進(jìn)行能量轉(zhuǎn)換,傳遞與控制的一種傳動(dòng)方式。液壓傳動(dòng)是以密封容器中的受壓氣體作為工作介質(zhì)來(lái)傳遞運(yùn)動(dòng)和動(dòng)力的傳動(dòng)。
根據(jù)帕斯卡原理和靜壓力的特性(在液壓傳動(dòng)系統(tǒng)中,靜止液體內(nèi)部各點(diǎn)的壓力處處相等),液壓傳動(dòng)不僅可以進(jìn)行力的傳遞,而且還能將力放大和改變力的方向。圖8-1所示為應(yīng)用帕斯卡原理推導(dǎo)壓力與負(fù)載關(guān)系的實(shí)例。
液力傳動(dòng)主要是利用液體動(dòng)能進(jìn)行能量轉(zhuǎn)換的傳動(dòng)方式,如液力耦合器和液力變矩器。液壓傳動(dòng)是利用液體壓力能進(jìn)行能量轉(zhuǎn)換的傳動(dòng)方式。
液壓傳動(dòng)的工作原理是:利用液體的壓力傳遞運(yùn)動(dòng)和動(dòng)力。先利用動(dòng)力元件將原動(dòng)機(jī)的機(jī)械能轉(zhuǎn)換成液體的壓力能,再利用執(zhí)行元件將體液的壓力能轉(zhuǎn)換為機(jī)械能,驅(qū)動(dòng)工作部件運(yùn)動(dòng)。以上就是液壓傳動(dòng)的工作原理。
液壓傳動(dòng)原理:機(jī)械能轉(zhuǎn)換為液體的壓力能 工作原理:電動(dòng)機(jī)帶動(dòng)液壓泵從油箱吸油,液壓泵把電動(dòng)機(jī)的機(jī)械能轉(zhuǎn)換為液體的壓力能。
液壓傳動(dòng)的基本工作原理是什么?
液壓傳動(dòng)是靠密封容器內(nèi)的液體壓力能,來(lái)進(jìn)行能量轉(zhuǎn)換,傳遞與控制的一種傳動(dòng)方式。液壓傳動(dòng)是以密封容器中的受壓氣體作為工作介質(zhì)來(lái)傳遞運(yùn)動(dòng)和動(dòng)力的傳動(dòng)。
以液體作為工作介質(zhì),并以其壓力勢(shì)能進(jìn)行能量傳遞的方式,即為液壓傳動(dòng)。力按照帕斯卡定律(靜壓傳遞定律)進(jìn)行傳遞。
液壓傳動(dòng)工作原理可用圖1-1所示的液壓千斤頂工作原理來(lái)說(shuō)明。圖中缸體3和柱塞4組成提升液壓缸;杠桿缸體柱塞7和單向閥9組成手搖動(dòng)力缸;2為控制閥;11和1分別為管道和油箱。
液力傳動(dòng)主要是利用液體動(dòng)能進(jìn)行能量轉(zhuǎn)換的傳動(dòng)方式,如液力耦合器和液力變矩器。液壓傳動(dòng)是利用液體壓力能進(jìn)行能量轉(zhuǎn)換的傳動(dòng)方式。
液壓傳動(dòng)的工作原理、系統(tǒng)組成是什么?
1、液壓傳動(dòng)系統(tǒng)由液壓動(dòng)力元件(液壓油泵)、液壓控制元件(各種液壓閥)、液壓執(zhí)行元件(液壓缸和液壓馬達(dá)等)、液壓輔件(管道和蓄能器等)和液壓油組成。
2、—杠桿手柄 2—小油缸 3—小活塞 4,7—單向閥 5—吸油管 6,10—管道 8—大活塞 9—大油缸 11—截止閥 12—油箱 大油缸9和大活塞8組成舉升液壓缸。
3、這就是液壓的基本原理。機(jī)械傳動(dòng)系統(tǒng)的組成 機(jī)械傳動(dòng)系統(tǒng)有以下四個(gè)主要部分組成:動(dòng)力部分,執(zhí)行部分,控制部分,***部分。動(dòng)力部分:把機(jī)械能換成油液壓力能,常見的是液壓泵。
4、先利用動(dòng)力元件將原動(dòng)機(jī)的機(jī)械能轉(zhuǎn)換成液體的壓力能,再利用執(zhí)行元件將體液的壓力能轉(zhuǎn)換為機(jī)械能,驅(qū)動(dòng)工作部件運(yùn)動(dòng)。以上就是液壓傳動(dòng)的工作原理。
5、液壓系統(tǒng)的作用為通過(guò)改變壓強(qiáng)增大作用力。一個(gè)完整的液壓系統(tǒng)由五個(gè)部分組成,即動(dòng)力元件、執(zhí)行元件、控制元件、***元件(附件)和液壓油。液壓系統(tǒng)可分為兩類:液壓傳動(dòng)系統(tǒng)和液壓控制系統(tǒng)。
6、液壓傳動(dòng)原理:以油液作為工作介質(zhì),通過(guò)油液內(nèi)部的壓力來(lái)傳遞動(dòng)力。動(dòng)力部分-將原動(dòng)機(jī)的機(jī)械能轉(zhuǎn)換為油液的壓力能(勢(shì)能)。例如:各種液壓泵。執(zhí)行部分-將液壓泵輸入的油液壓力能轉(zhuǎn)換為帶動(dòng)工作機(jī)構(gòu)的機(jī)械能。
1.何謂液壓傳動(dòng)?其基本工作原理是什么?
1、液壓傳動(dòng)是以密閉管路中的受壓液體為工作介質(zhì),進(jìn)行能量的轉(zhuǎn)換、傳遞、分配和控制的技術(shù)。液壓傳動(dòng)工作原理可用圖1-1所示的液壓千斤頂工作原理來(lái)說(shuō)明。
2、液壓傳動(dòng)是以密閉管路中的受壓液體為工作介質(zhì),進(jìn)行能量的轉(zhuǎn)換、傳遞、分配和控制的技術(shù),稱之為液壓技術(shù),又稱液壓傳動(dòng)。液壓傳動(dòng)的原理主要以帕斯卡原理、液體連續(xù)性原理和能量守恒定律為主,詳細(xì)的可以查看一下液壓傳動(dòng)教材。
3、液壓傳動(dòng)基本原理 如圖2-62所示為一簡(jiǎn)化的液壓傳動(dòng)系統(tǒng),其工作原理如下: 液壓泵由電動(dòng)機(jī)驅(qū)動(dòng)旋轉(zhuǎn),從油箱經(jīng)過(guò)過(guò)濾器吸油。
4、液壓傳動(dòng)系統(tǒng)的基本原理:液壓傳動(dòng)是利用密閉系統(tǒng)中的受壓液體來(lái)傳遞運(yùn)動(dòng)和動(dòng)力的一種傳動(dòng)方式。
5、液力傳動(dòng)主要是利用液體動(dòng)能進(jìn)行能量轉(zhuǎn)換的傳動(dòng)方式,如液力耦合器和液力變矩器。液壓傳動(dòng)是利用液體壓力能進(jìn)行能量轉(zhuǎn)換的傳動(dòng)方式。
關(guān)于機(jī)械液壓傳動(dòng)基本原理和機(jī)械基礎(chǔ)液壓傳動(dòng)課程的介紹到此就結(jié)束了,不知道你從中找到你需要的信息了嗎 ?如果你還想了解更多這方面的信息,記得收藏關(guān)注本站。
[免責(zé)聲明]本文來(lái)源于網(wǎng)絡(luò),不代表本站立場(chǎng),如轉(zhuǎn)載內(nèi)容涉及版權(quán)等問(wèn)題,請(qǐng)聯(lián)系郵箱:83115484@qq.com,我們會(huì)予以刪除相關(guān)文章,保證您的權(quán)利。轉(zhuǎn)載請(qǐng)注明出處:http://www.nmgwu.com.cn/post/25350.html發(fā)布于 -60秒前